New research shows 93% of building operability issues identified in VR aren’t caught with traditional construction coordination methods
A new research paper published in the ASCE journal on Computing in Civil Engineering shows that that 93% of the operability issues found in VR reviews of BIM were not found by traditional methods.
In the fast-paced world of construction, immersive technologies are quickly turning from nice-to-haves into scientifically proven necessities. A recent paper published in the American Society of Civil Engineering’s (ASCE) journal on Computing in Civil Engineering demonstrates that using virtual reality (VR) in design reviews can help reduce the cost of rework, requests for information (RFIs), and change orders associated with operability issues.
The paper compared design coordination methods on a $600M project, finding that 93% of the operability issues found in VR were not found by traditional methods.
These results echo real-world case studies showing the efficacy of VR in reducing construction costs. We recently spotlighted how Fortis Construction saved millions using VR and how Mortenson spots critical issues using VR.
Through a comparative case study on 2 buildings of the same facility project, the study quantifies the impact of VR on the early identification of operability issues during MEP coordination.
In Building 1, VR was not implemented during MEP coordination, whereas in Building 2, the project team implemented VR using Resolve with Meta Quests. We were excited to see the project team chose Resolve and the Meta Quest as their virtual reality platform of choice to review building models before construction was complete.
The research paper, titled Construction Cost Savings through VR-Based Early Identification of Operability Issues: A Comparative Case Study, offers valuable insights discussed in this post. The full paper can be purchased and accessed on the ASCE website:
Bridging the Gap in Construction Reviews
Although the review of 3D building information models (BIM) on 2D monitors is a standard practice, it has many limitations. Traditional reviews primarily reveal clash and constructability issues while saying little about whether a building can be operated efficiently and safely. Unaddressed, these operability issues can cause cost of ownership to skyrocket.
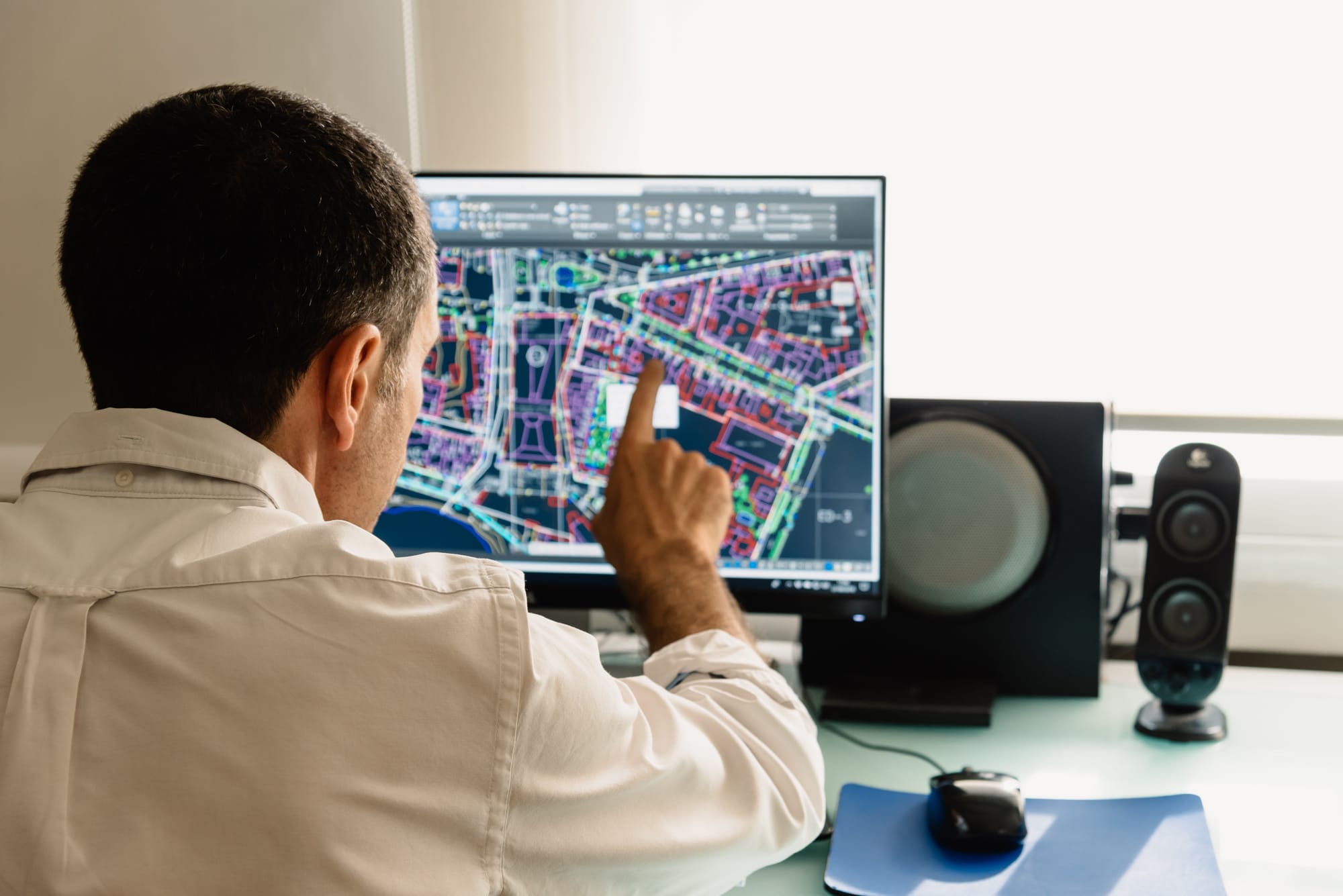
Led by BIM and virtual design and construction (VDC) teams, today’s coordination reviews rely on input from facility operations and maintenance staff to flag operability concerns during model coordination.
This workflow puts the onus on facility operators to reliably flag operability issues. This is challenging for a few reasons:
- Facility operators don’t spend all day in Navisworks or other BIM tools, so their capacity to efficiently identify issues in 3D software is limited.
- Facility operators have ongoing work tending to existing facilities, so their bandwidth to comb through models and drawings for issues is limited.
- Facility operators have the field experience needed to quickly identify potential issues but limited ability to apply this experience until the building exists
Since it’s difficult to detect operability issues on a 2D screen, it becomes critical to conduct thorough field inspections during commissioning. At that point, any issues found have a much higher cost to address since installation has already occurred.
Enter VR. The research paper cites several studies, starting as early as 2014, which have shown that VR can help with more efficient issue identification during BIM reviews. However, the use of VR has been held back by limitations in hardware and software. New developments in standalone, accessible hardware like Meta Quest and easy-to-use software like Resolve present new opportunities to revisit the impact that VR can have on detection of operability issues. .
A Groundbreaking Study
The study involved a detailed comparison over five months on two similar buildings of a $600M construction project. The project required LOD 400 MEP coordination models and the detailed models were used to collect feedback from facility operators during MEP coordination in preconstruction.
One unique aspect of this research is the more accessible method used to collect feedback from operations participants. Past research on VR only allowed participants access to VR during key review meetings. Historically, VR hardware setups were tethered, so usage was in conference rooms and the people providing feedback could only access it during meetings.
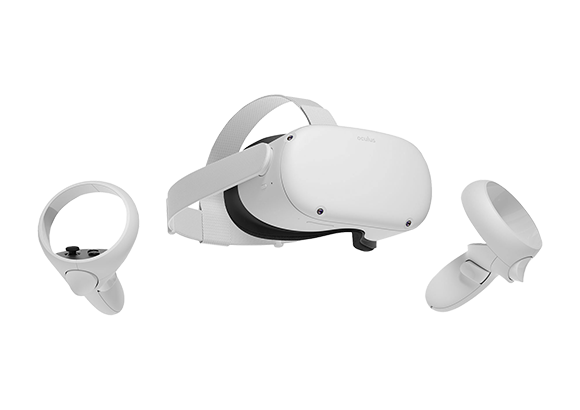
The study utilized personal VR headsets, specifically the Meta Quest 2 paired with Resolve VR software. At Resolve, we’ve always been firm believers that VR devices should be treated like personal computers. This unlocks engagement by enabling facility operators to conduct reviews at their convenience, without the need for formal scheduling.
This flexibility, only made possible by recent developments in technology, marked a significant departure from previous studies, where VR usage was confined to the times everyone was able to meet.
The study mentions the facility project team’s selection of tools:
“Meta Quest 2 VR headsets and Resolve VR software were used based on affordability, setup ease, user experience, and ability to import 3D models that are above 1GB.”
Girgin et al. (2023)
Another element that further sets this study apart from earlier research is its comprehensive approach and the unique opportunity to compare two similar buildings—one with VR used in the MEP coordination process and one without.
To recap here is what we think makes this research novel:
- Scientific control: This is the first study to scientifically evaluate the impact of VR on construction processes by comparing similar projects with and without the technology. Such a direct comparison is rare in construction, making the findings particularly valuable.
- Individual accessibility: By providing individual access to VR technology, the study expanded the potential for engagement and feedback beyond traditional, scheduled review sessions. This approach allowed for more flexible and frequent reviews to help with data collection.
- Quantifiable impact: The research not only highlighted the effectiveness of VR in identifying operability issues but also quantified the differences in issue detection and cost savings compared to traditional coordination software, providing a compelling case for the technology's ROI in construction projects.
Key Findings
The results are significant. VR allowed for the identification of operability issues that impact late-stage rework, RFIs, and change orders.
93.4% of the operability issues discovered in VR had not been previously identified with traditional coordination methods.
To us, this emphasizes how valuable VR can be for detection of issues beyond constructability. VR can reduce the risk of issues during post-construction operations of a building which is the majority of the building’s existence.
“the identification of 86 previously unidentified issues added value to the MEP coordination process by increasing the quality of the facility design and, more importantly, preventing issues during the building’s operations phase.”
Girgin et al. (2023)
While it’s possible that these issues are caught during field walks, the cost of making changes during a field walk is significantly higher than correcting an issue during the digital coordination process.
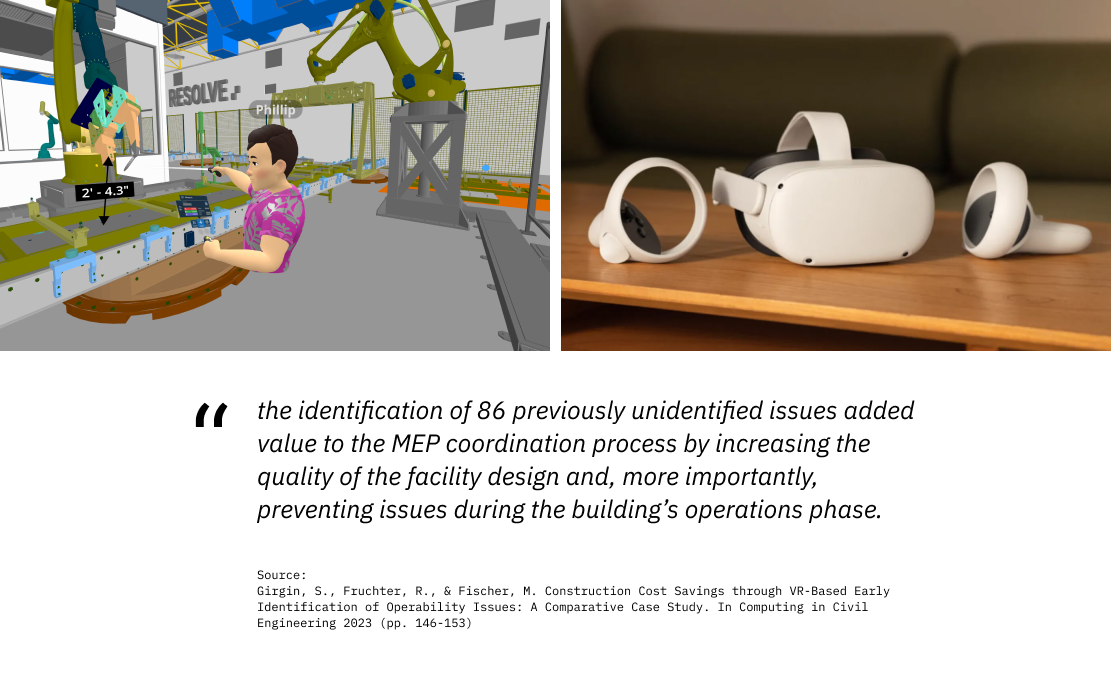
The operability issues found in VR for Building 2 were compared to the operations issues that were flagged during field inspections of building 1, and significant similarities were observed. We think this speaks to the power of VR to give people an accurate representation of the final product without needing to physically build it or be present at the site.
“The comparison of the field-detected issues, RFIs, and change orders documented for Building 1 to the operability issues identified in VR for Building 2 reveals that significant MEP-related construction field rework, RFIs, and change orders could have been avoided.”
Girgin et al. (2023)
The research also analyzed the operability issues detected in VR, with an estimated cost savings of $107,443 for 89 issues. This analysis was conducted by breaking down the associated costs with rework, RFIs, and change orders associated with the various issues.
This represents a significant ROI for VR on construction projects. And beyond the quantified cost savings of each issue, we believe it’s important to note the reduced operations risk after turnover for the rest of the building lifecycle. The savings estimated by the study focused on operability and only captured a fraction of the total ROI of using VR throughout design and construction. In our work with other projects we have seen savings upwards of $3M in just 3 months.
Embracing the Future with VR Technology
For Resolve, this published research is a beacon, highlighting the immense impact that VR has on construction outcomes. The technology has matured beyond the stage of only being valuable for marketing demos or hypothetical cost savings. With advancements in technology powered by Resolve’s Wellington Engine, the ROI can easily be scaled to more people and more projects.
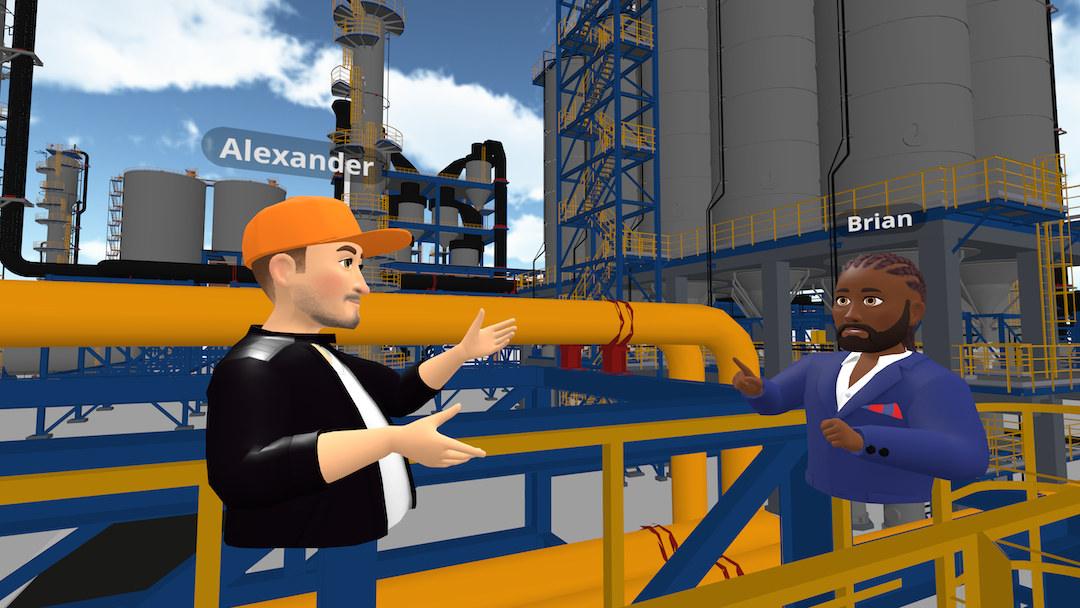
In addition to encouraging construction teams to leverage VR on their next project, we also hope this study gives teams the confidence to expand usage of VR beyond VDC experts. From this study it’s clear that when facility and owner staff are empowered with this technology they too can provide valuable feedback that results in cost savings and a happier client.
This research underscores the value of VR in construction, offering a tangible example of how the technology can lead to more efficient, cost-effective, and higher-quality outcomes.
Summary of takeaways:
- The study shows 93% of operability issues found in VR are not being found with traditional tools like Navisworks
- The issues found in VR reduce cost of construction by reducing rework, RFIs, and change orders. 89 operability issues found in VR saved $107,443 in rework, RFIs, and change orders.
- VR is usable by operations and maintenance staff so that they can provide key feedback about operability concerns during coordination
VR for construction has matured beyond proof of concept
The integration of VR into construction processes represents a significant leap forward in ensuring operability and avoiding costly operational issues down the line. As "Construction Cost Savings through VR-Based Early Identification of Operability Issues: A Comparative Case Study" by Girgin et al. (2023) shows, the benefits of VR in early identification of operability issues are immense.
Reference:
Girgin, S., Fruchter, R., & Fischer, M. Construction Cost Savings through VR-Based Early Identification of Operability Issues: A Comparative Case Study. In Computing in Civil Engineering 2023 (pp. 146-153).
Do you want to upload your own BIM to review in VR? Sign up for a free trial.
Resolve builds software that makes 3D building information models more accessible so teams can find critical issues that save time and money on new construction. Resolve's Wellington Engine can render large BIM files on the standalone VR devices making it a scalable, easy to use solution for project teams. Resolve is used by leaders spanning industries like food & beverage, water treatment, data centers, biopharmaceuticals, and green energy.